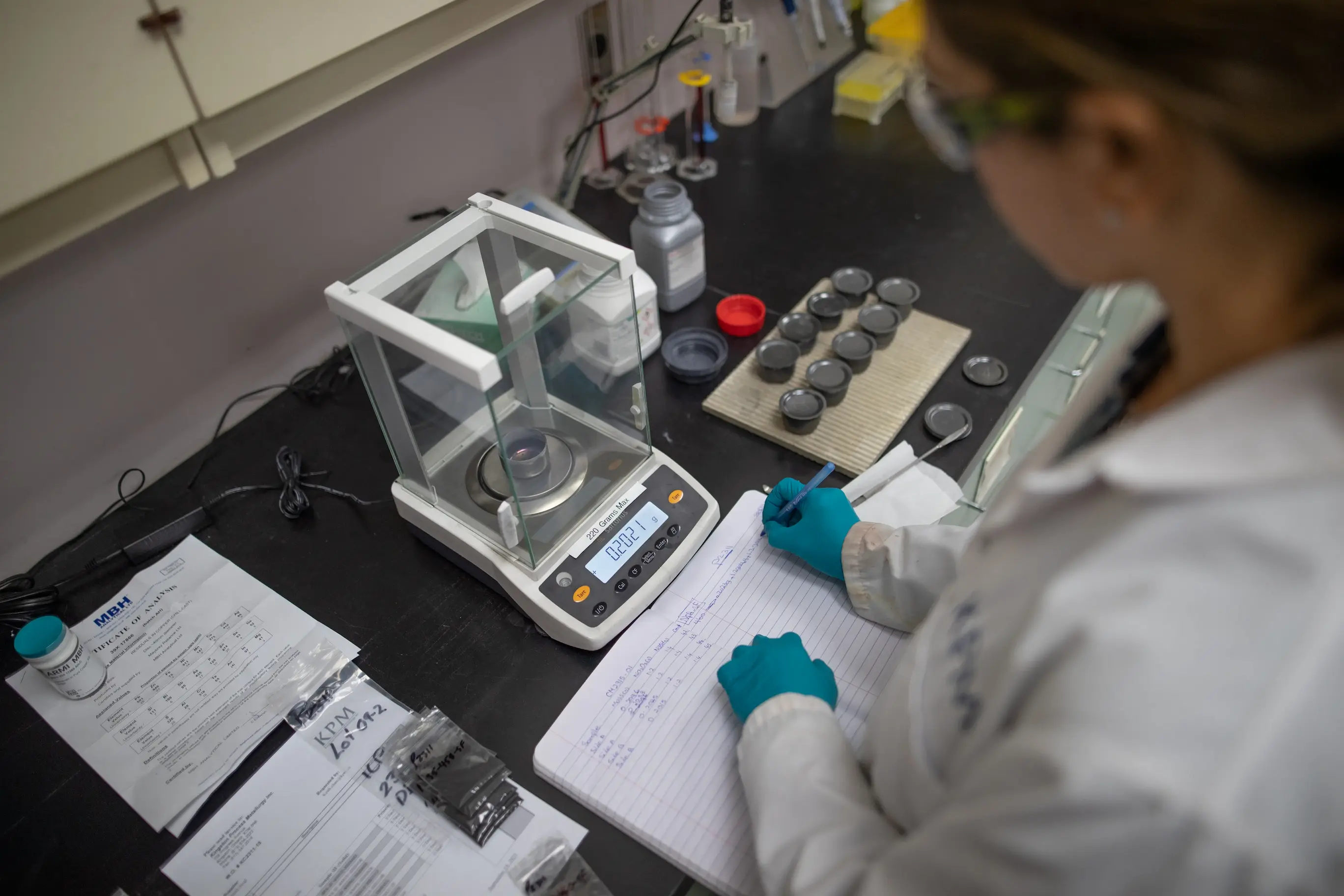
Services
Techno-Economic Analysis (TEA) Studies & Computer Modeling
Techno-Economic Analysis (TEA) studies and computer modeling are key components of the services at KPM and are fundamental for planning the experimental work and for designing new processes and equipment. Essential to the successful development of a process is the early identification of the key economic drivers, evaluation of the full-scale project implementation costs (CAPEX/OPEX), the generation of a detailed process flow diagram (PFD), and preparation of the associated technology package documents. This TEA can then be used to identify the key missing technical information and direct laboratory work required in order to tackle the aspects with the greatest impact on the project viability. Sensitivity analysis is integral part of this work.
Without the direction provided by computer modeling, including thermochemical equilibria (FACT-SAGE) and heat and mass balance (SysCAD), development can only be made through physical trial and error which is costly and impractical. Modeling also allows for the extrapolation of important data from bench-scale or pilot tests to larger scale processes.
It is the way KPM combines techno-economic studies, computer modeling, and experimental work that allows us to provide the best value and the fastest turn-around from concept to implementation. We enjoy working on chemistry, but it is the economic potential of a proposed process or process modification that guides our work.
TEA and computer modeling support project work at KPM by:
- Evaluating the technical and economic viability of a project
- Providing an early evaluation of the CAPEX and OPEX
- Improving fundamental knowledge of chemistry involved in process
- Facilitating design of experiments
- Evaluating experimental results
- Generating property measurements
- Developing process controls and optimization
- Developing a process design package
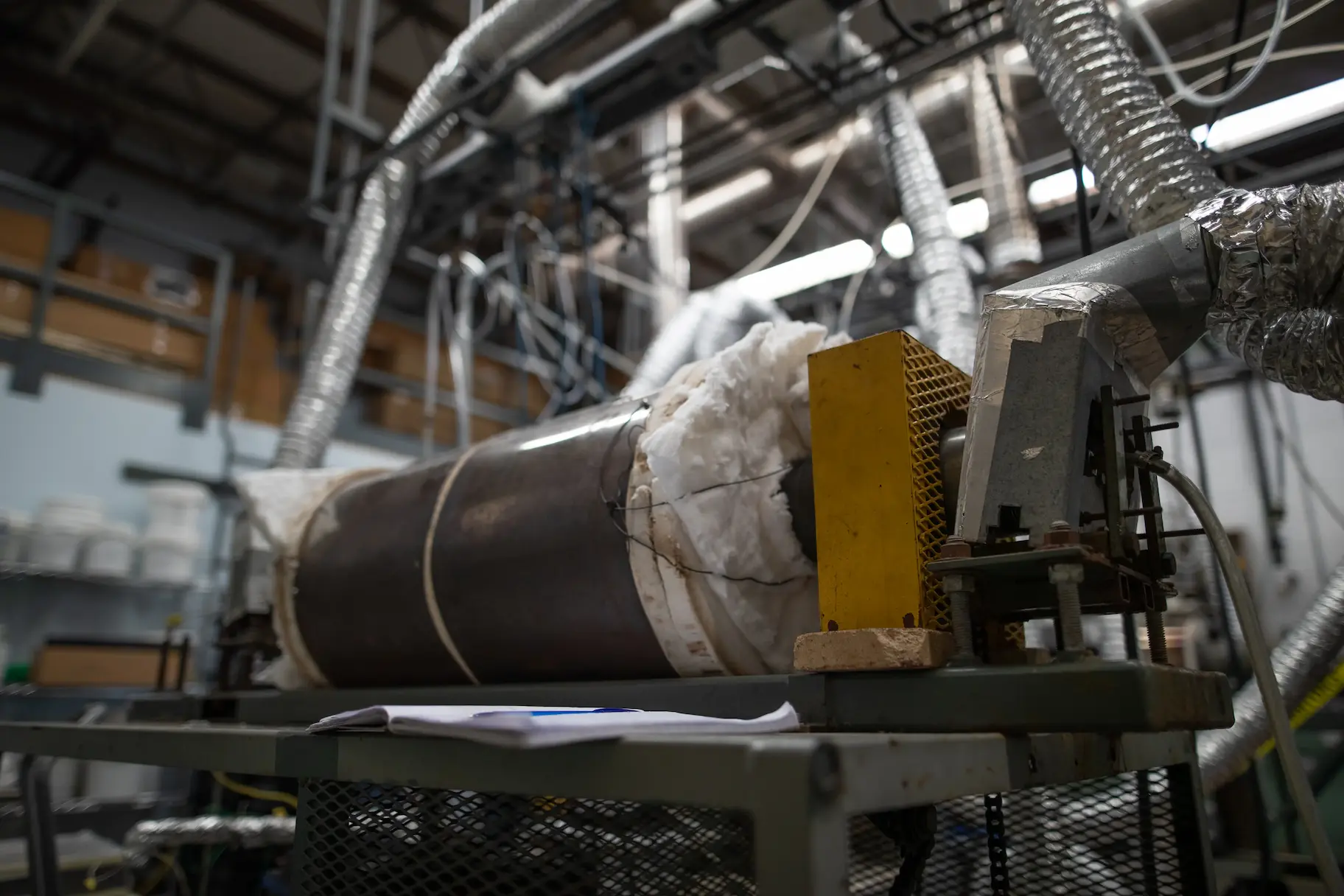
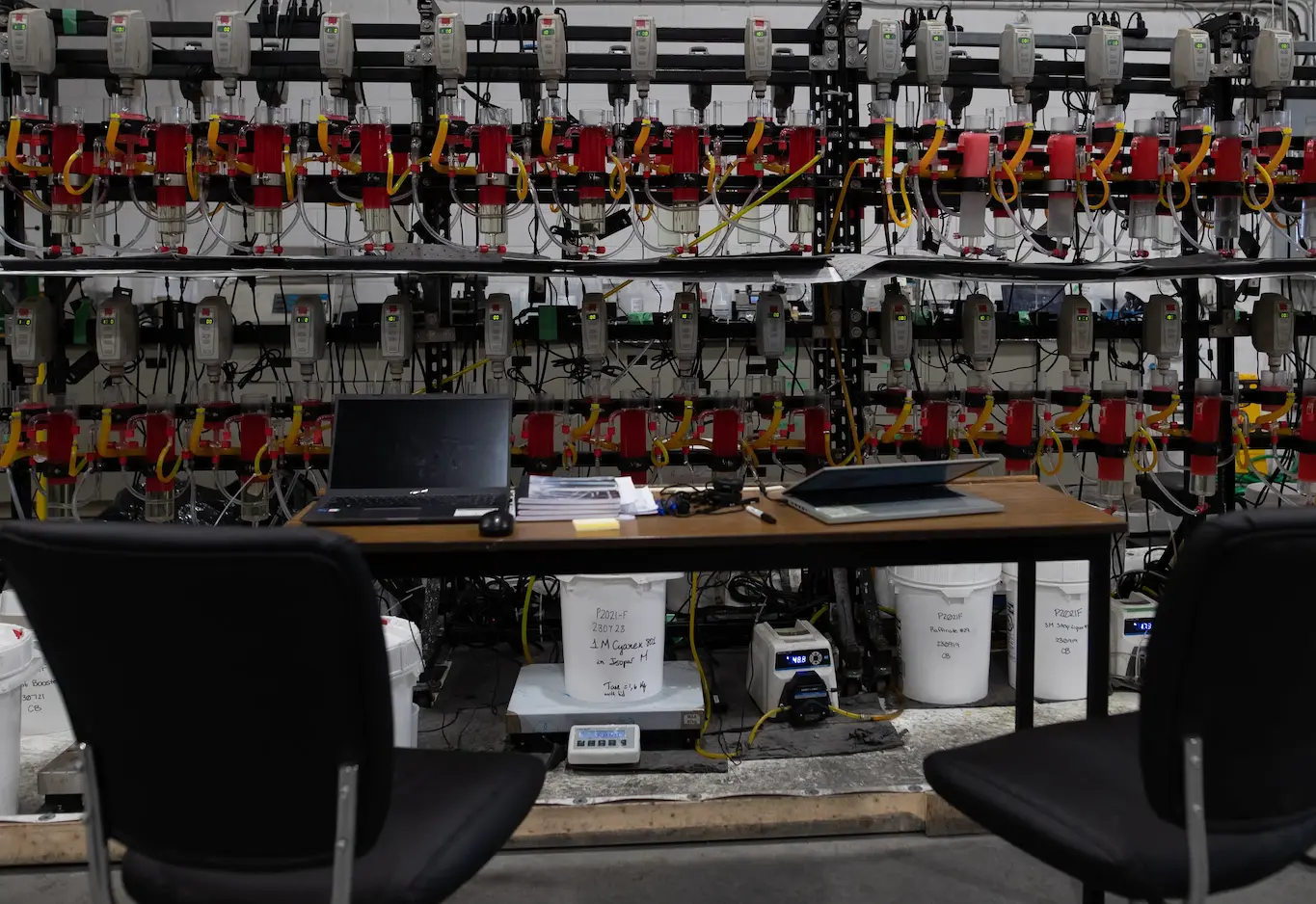