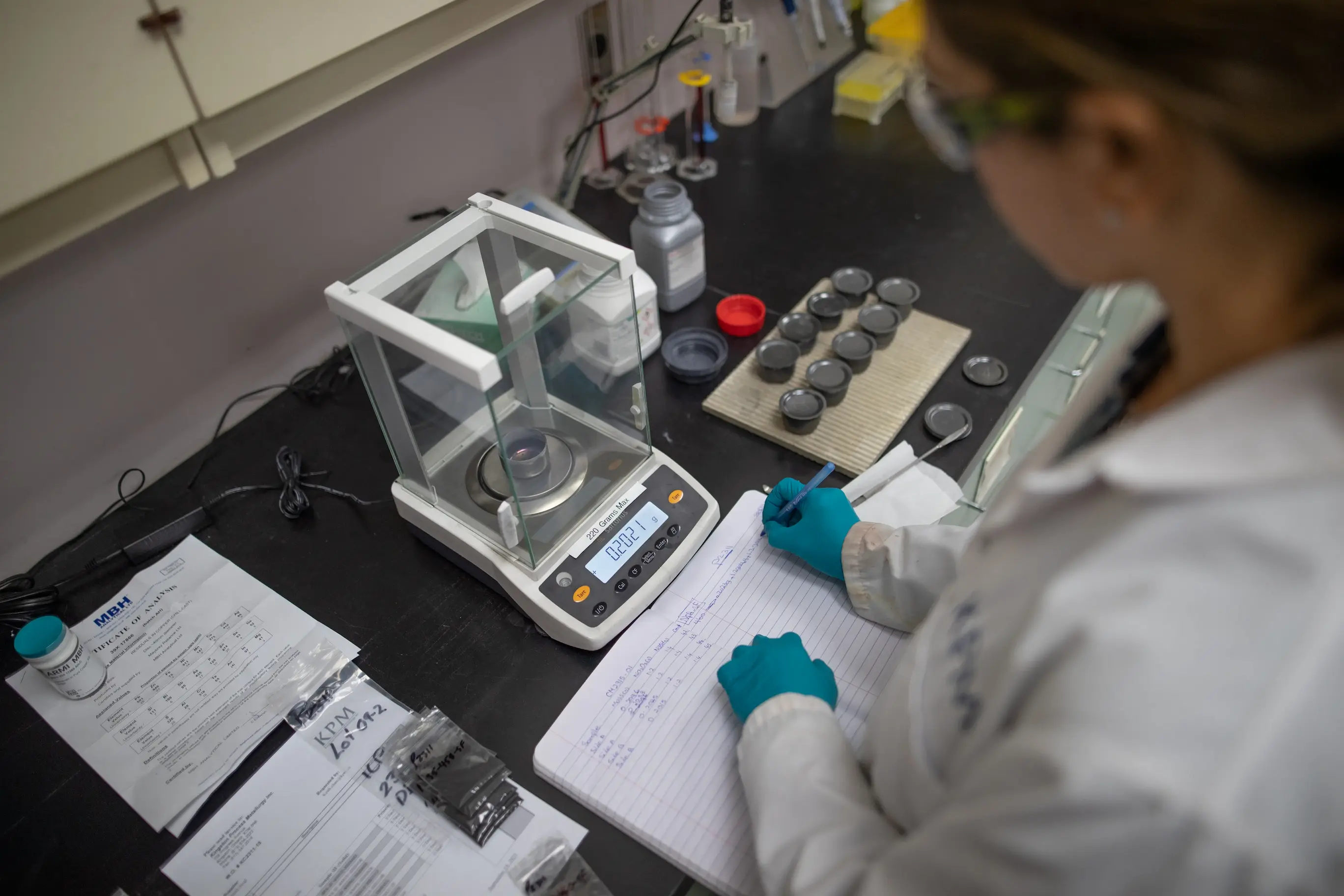
Services
Integrated Process Development
The core of the company's activities is client-driven experimental research for process development and optimization. We specialize in experimental design, bench-scale laboratory work, mini-pilot campaigns, flow sheet development, unit operation selection, process modeling, and scale-up to demonstration pilot plants. Our goal is to provide clients with Clarity on process designs that will meet their needs, based on solid techno-economic analysis.
KPM works on a very wide range of processes and materials, largely related to primary and secondary metal production, environmental protection, and a variety of clean-tech opportunities.
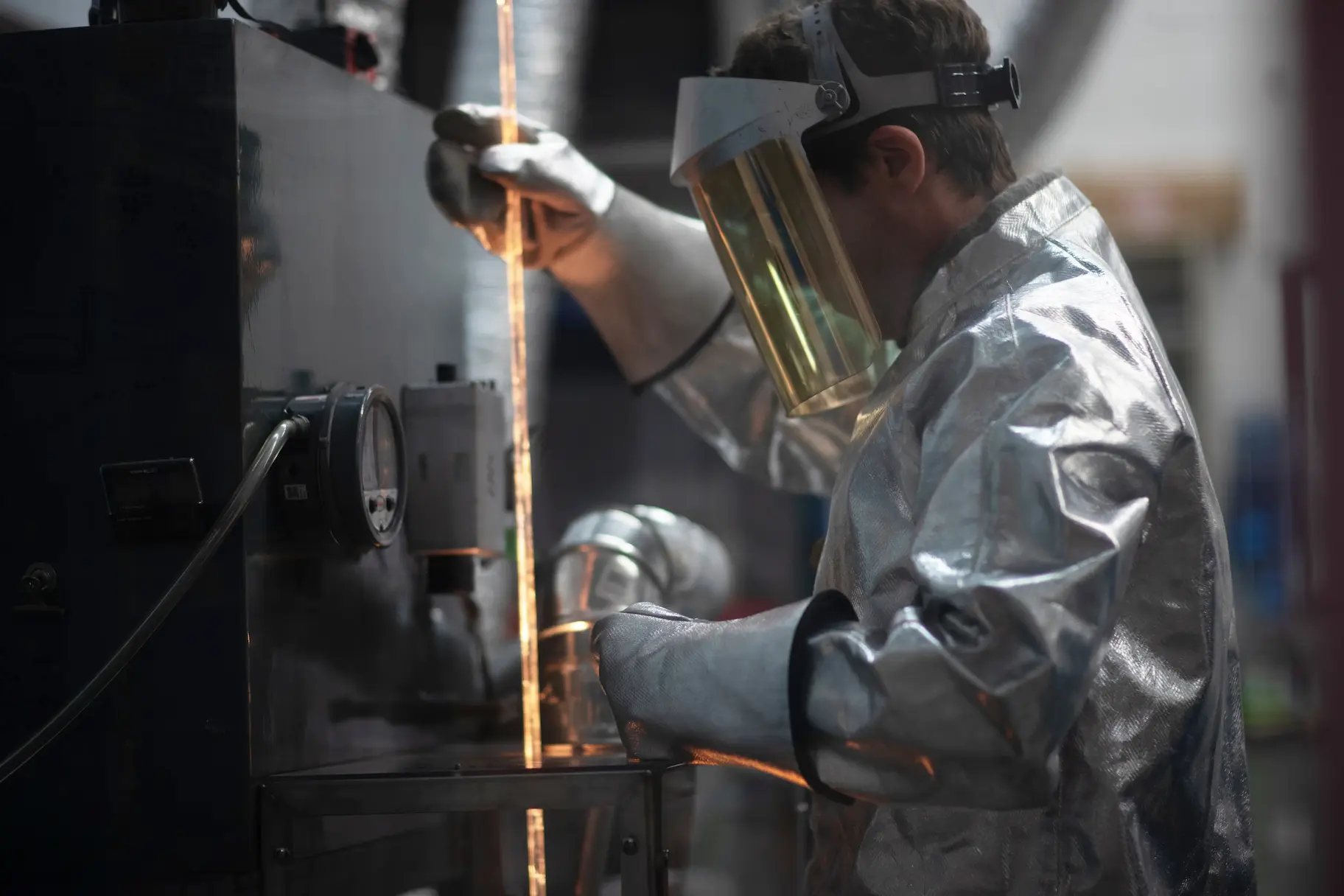